TUNNEL
washers are designed for continuous cleaning of mechanical parts
using water base detergents and are typical for single or multi-stages
process with a high throughput. Parts can be processed singly
or in batches.
TUNNEL
washers are commonly used in the production lines of the mechanical,
automotive and aerospace industry either for interprocess or final
cleaning. For their flexibility they are suitable to mass or limited
production.
|
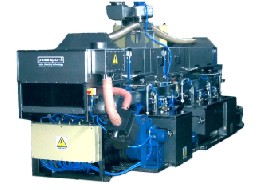
|
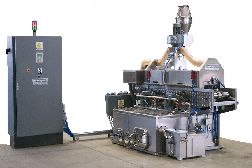 |
The
operating principle is based on a linear movement through
the process: parts are carried through the different phases
of the process at the proper speed.
Parts can be moved in continuous or indexed for precision
cleaning of holes and recesses. Conveyors
can be configured in many ways: with a belt or chains, to
carry, pull or push the parts, pallets or baskets and with
fixtures for specific applications.
|
Processes, single
or multistage, that can be carried out by TUNNEL washers
are all those for wash, rinse, phosphodegreasing, passivation,
protection, blow-off, drying, cooling. Machines
with small footprint and extremely compact have been developed
to fit process lines in the automotive industry. For that, specific
techniques have been developed: conveyors with specific characteristics
to minimize drag out of liquids, drying systems with and without
heating, compact systems for heating, ventilation and filtration.
Using new technologies PASSAPONTI has also developed drying systems
based on the air knife technique that can reach 70°C without
heating elements or using compressed air but with very low
consumption and noise below 70 dBA.
TUNNEL
washers are equipped with forced ventilation to capture vapours
with very low energy consumption and usable with the mist eliminator
RETEN-MIST®or
the vapour condenser VAPOR-MIST®avoiding
the cost of ducts to the external.
TUNNEL
washers are composed by a robust self contained, floor mounted
structure with the conveyor, tanks, spray system and all the relevant
equipment. The conveyor is driven by a gearmotor with torque limiter,
adjustable speed and automatic controls and safety equipment.
The
spray system is composed by the pump and the spray headers with
quick disconnect calibrated nozzles. Special care is dedicated
to maintenance with easy access to all parts. Before entering
the tank the wash liquid passes through a gravity-fed filter easily
accessible for cleaning.
To
reduce drag out of the liquids, process stages are separated by
vestibules with curtains.
Tanks
with heating are insulated with mineral wool and equipped with
a filter, drain out valve, marine type clean out door, overweir,
low level cut out, and additional facilities such as the automatic
oil separator OILNET®,
bag or cartridge filters and more. |